Precision Carpentry Services for Homes & Businessesin Woodstock GA
Skilled Craftsmanship for Framing, Trim, and Custom Builds
We Are Locally Owned & Operated For Over 24 Years
We Serve Businesses In And Around The Following Cities:
About Carpentry in Woodstock, Georgia
Carpentry in Stucco, EIFS, and Dryvit Installation and Repair in Woodstock, Georgia
Understanding the Role of Carpentry in Exterior Systems
Carpentry is often associated with framing houses or creating fine woodwork, but its significance extends far beyond traditional residential bounds. Especially in Woodstock, Georgia, where both residential neighborhoods and commercial complexes blend suburban charm with modern architectural trends, the fusion of carpentry with exterior cladding systems—such as stucco, EIFS (Exterior Insulation and Finish Systems), and Dryvit—brings both functional and aesthetic value. The skilled integration of carpentry into the installation and repair of these exterior finishes ensures that structures remain both visually appealing and structurally sound.
Whether it's prepping for a flawless stucco installation or replacing compromised sheathing behind Dryvit during a repair, the marriage of finish and rough carpentry with façade systems is essential. This is exactly where the expertise of Advanced Stucco Repair stands out. By combining deep knowledge in exterior cladding with carpentry proficiency, they help home and business owners in Woodstock maintain the condition, value, and beauty of their properties.
Why Carpentry Matters in Stucco and EIFS Systems
At first glance, stucco and EIFS appear to be independent of woodwork. However, beneath the surface lies a framework dependent on strategic carpentry. During a new stucco application, rough carpentry creates the foundation for the system to be mounted correctly. Proper framing ensures flatness, stability, and durability, while addressing key design considerations like moisture control and drainage. In Woodstock’s variable climate—with hot summers and high humidity—precise framing prevents warping, buckling, or moisture entrapment behind stucco finishes.
In repair situations, particularly when dealing with water intrusion, the scope often extends beyond surface patching. Damaged sheathing, rotten studs, or framing inconsistencies must be corrected before the exterior is reapplied. This is where custom carpentry plays a vital role in restoring the building envelope. Advanced Stucco Repair often uncovers unexpected issues beneath decaying surfaces, and their trained team blends exterior system expertise with refined carpentry to complete both cosmetic and structural repairs seamlessly.
EIFS and Dryvit, being synthetic stucco systems, rely even more heavily on a stable substructure. The foam insulation boards used in these systems must be laminated to a smooth, sturdy surface. Finish carpentry techniques often come into play, rounding window trims, framing doors, and integrating ventilated reveals. The alignment of these synthetic components is crucial both for water management and aesthetic lines, and imperfect carpentry work can lead to future failures or noticeable deformations in the building's visual plane.
The Process – From Inspection to Completion
Every successful stucco or EIFS installation or repair in Woodstock begins with a detailed assessment. Advanced Stucco Repair typically starts by inspecting the structure’s current state, taking note of prior installations, damages, and underlying framing conditions. For older buildings, gypsum sheathing or OSB might have weakened. Here, carpentry becomes the keystone in restoring a stable base. Rotten wood is removed, and new framework is meticulously assembled to match the original layout or to meet modernized building codes.
When dealing with repairs, especially prevalent in Woodstock’s older commercial plazas or in dated residential developments, a common issue is the stretching or detachment of the finish layer. Behind this, the wooden subframe may be decaying. In these cases, precise rough carpentry is required to rebuild the sheathing and joists or even reconstruct parts of the wall’s framework. This is often accompanied by door framing corrections—especially when threshold rot is found—or dealing with misaligned windows, which may require custom woodwork to adapt to the new stucco contours.
The next stage is framing for reinstalling stucco or Dryvit. Gaps must be sealed, framing corners must be braced—particularly around windows, where water accumulation is frequent. As part of EIFS repairs, trained carpenters often integrate back-wrapping procedures and install new foam panels that need a steady, aligned surface behind them. Once the structural carpentry is complete, application teams move in to begin layering base coats, reinforcing mesh, and finishing with acrylic or textured finishes. Even at this point, carpentry contributes through things like crown molding installation at eaves and integrating casing beads around doors and vents.
Advanced Stucco Repair’s distinctive approach lies in integrating skilled trades under one roof—this eliminates miscommunication between subcontractors and ensures continuity. Their team understands how a miscut piece of sheathing or misaligned corner bracing can affect the finish of the entire stucco wall. From structural straightening to enhanced finish detailing, their carpentry work drives the reliability of exterior envelope solutions.
Enhancing Aesthetics and Functionality with Expert Carpentry
Beyond foundational work, carpentry in exterior systems enhances the beauty and cohesion of a building’s envelope. In residential settings throughout Woodstock's picturesque subdivisions—like Towne Lake and Downtown Woodstock—homeowners are often drawn to refined architectural details. Here, finish carpentry and precision molding help achieve desired aesthetics. Whether integrating custom trim around decorative stucco arches, or installing crown molding along gables and eaves, ornamental detailing adds value and curb appeal.
Likewise, homes with Mediterranean or modern aesthetics—which frequently utilize stucco or Dryvit exterior designs—benefit significantly from expert carpenters who understand how to cleanly execute design edges, balance symmetry, and blend exterior contours with windowsills, patios, and stone veneers. At Advanced Stucco Repair, carpentry isn’t just technical—it’s artistic. They offer custom woodwork solutions that rise to design challenges, such as blending traditional Georgian trims with contemporary European-finishes.
In commercial parks across Woodstock—such as those along Highway 92 or around the Outlet Shoppes—EIFS and Dryvit dominate exteriors due to their insulation and low maintenance benefits. These structures are highly visible, and imperfections detract from brand identity. Correcting damage from forklifts, impact from deliveries, or water leaks requires not only surface leveling, but coordinated carpentry to replace foundational panels, adjust framing, and reshape elements like signage cut-outs or loading bays. Here, precision matters down to every line.
Advanced Stucco Repair often tailors carpentry enhancements during EIFS upgrades that include mechanical integration—be it mounting new signage, creating HVAC cut-outs or overhauling storefront window structures. Flawless transitions between shaped foam moldings and existing architecture rely on individualized wood framing and skilled joinery. Without cohesive design knowledge, these additions may appear jagged or improperly balanced—a frequent issue when general contractors overlook the carpentry discipline within façade repairs.
Weather Resistance Through Integrated Framing Techniques
Woodstock’s climate presents its own challenges. Humidity fluctuations, occasional storm surges, and high UV exposure all take their toll on exterior systems. A crucial factor for long-lasting stucco or EIFS applications is weather-tight framing. Incorrect carpentry can create penetrable points where moisture intrudes and festers behind cladding. Critical to this is the correct installation of flashing, window framing, and roofline molding—all tasks demanding experienced carpentry.
Advanced Stucco Repair ensures framing is not only plumb and square, but also treated or flashed where necessary. Special attention is given to decks, chimneys, and bay windows—areas known for complex joints and water susceptibility. For instance, they often rebuild door-framing elements with treated lumber and integrate moisture barriers within carpentry layers. In EIFS applications, combining carpentry with routed drainage systems allows accumulated moisture to escape, significantly extending the lifespan and efficiency of the exterior envelope.
During repairs, it's not unusual for their carpentry teams to disassemble paneled sections of walls, replace substrate wood, and rebuild components from scratch. These repairs are critical in restoring complete envelope integrity, especially for investment properties where rot could decrease resale value. Framing corrections are also vital before applying leveling coats; otherwise, rippling shadows or finish separation might occur over time.
Long-Term Value of Professional Carpentry-Integrated Systems
When carpentry is performed without consideration for exterior finishes—or vice versa—homeowners and building managers face recurring problems, including cracking stucco, shifting EIFS foam panels, and wall leaks. Conversely, when these elements are planned cohesively, as done by Advanced Stucco Repair, structural strength complements façade beauty.
In many Woodstock-area residences and commercial locations, owners report massive savings in maintenance and repairs when composite carpentry-framed systems are installed correctly from day one. Good carpentry ensures flat substrates that reduce stress on stucco or Dryvit layers, especially around corners and openings. Custom framing eliminates awkward transitions, reducing the chances of delamination or thermal movement.
Whether you're a property manager overseeing a large plaza looking to refresh an aging façade or a homeowner wanting to fix unsightly cracking along your entryway columns, integrating high-level carpentry into stucco and EIFS projects yields dividends well beyond aesthetics. It improves lifespan, minimizes rework, and enhances building value—key benefits for discerning Woodstock residents who appreciate craftsmanship and durability.
Real-World Applications and Project Examples
Consider the multi-unit shopping center on the outskirts of Woodstock that faced persistent water intrusion and crumbling plaster. Attempts by general contractors to repair the surface failed repeatedly, until the owners engaged Advanced Stucco Repair. Their team investigated and found that interior wood blocking behind window returns had degraded. Using precision carpentry, they replaced compromised elements, rebuilt soffits with crown molding installation, and reapplied EIFS with sloped reveals for drainage. The result was both structurally and visually transformative.
In a residential case, a custom home in Downtown Woodstock suffered from bubbling stucco and crooked window sills. Examination revealed that the under-frame around doorways and beneath window trims was misaligned. Advanced Stucco Repair rebuilt these sections using seasoned carpenters who placed shims strategically, realigned trims, and applied fresh Dryvit with perfection. Now, the property enjoys improved energy efficiency and a modernized façade that complements the area’s charm.
Even in small-scale projects like porch refacing or decorative arch rebuilding, the value of integrated carpentry shines through. A recent project along Arnold Mill Road saw a unique blend of custom woodwork supporting hand-carved foam moldings. Finished with acrylic stucco, the property now stands out with its tailored European styling, achieved by balancing architecture with warm craftsmanship.
Refining Your Next Exterior Project Through Craftsmanship
Ultimately, it’s clear that thoughtful carpentry forms the backbone of any successful stucco, EIFS, or Dryvit project—especially in Woodstock, where impeccable curb appeal and durable exteriors are increasingly demanded. Whether enhancing a storefront’s allure or restoring a home’s weathered corners, strategically blending finish and rough carpentry into cladding systems ensures both beauty and long-term reliability.
Residents and business owners seeking high-quality, low-maintenance exterior solutions should consider not only the surface appearance but the supporting structure. Partnering with a company experienced in both carpentry and stucco systems—such as Advanced Stucco Repair—offers assurance that every layer, from wall framing to final finish, is executed with care and skill. Their team doesn’t just treat symptoms—they resolve problems at their core, rebuilding from a place of craftsmanship and integrity.
Whether you're considering a fresh EIFS façade for your commercial building, repairing cracked stucco on your family home, or incorporating stylish crown molding into a rebuilt porch, aligning with a service provider who treats carpentry as an integral component of the project will elevate both results and satisfaction. In Woodstock, Advanced Stucco Repair continues to be trusted by those who value expertise, precision, and lasting beauty in their exterior renovations.
Carpentry Gallery
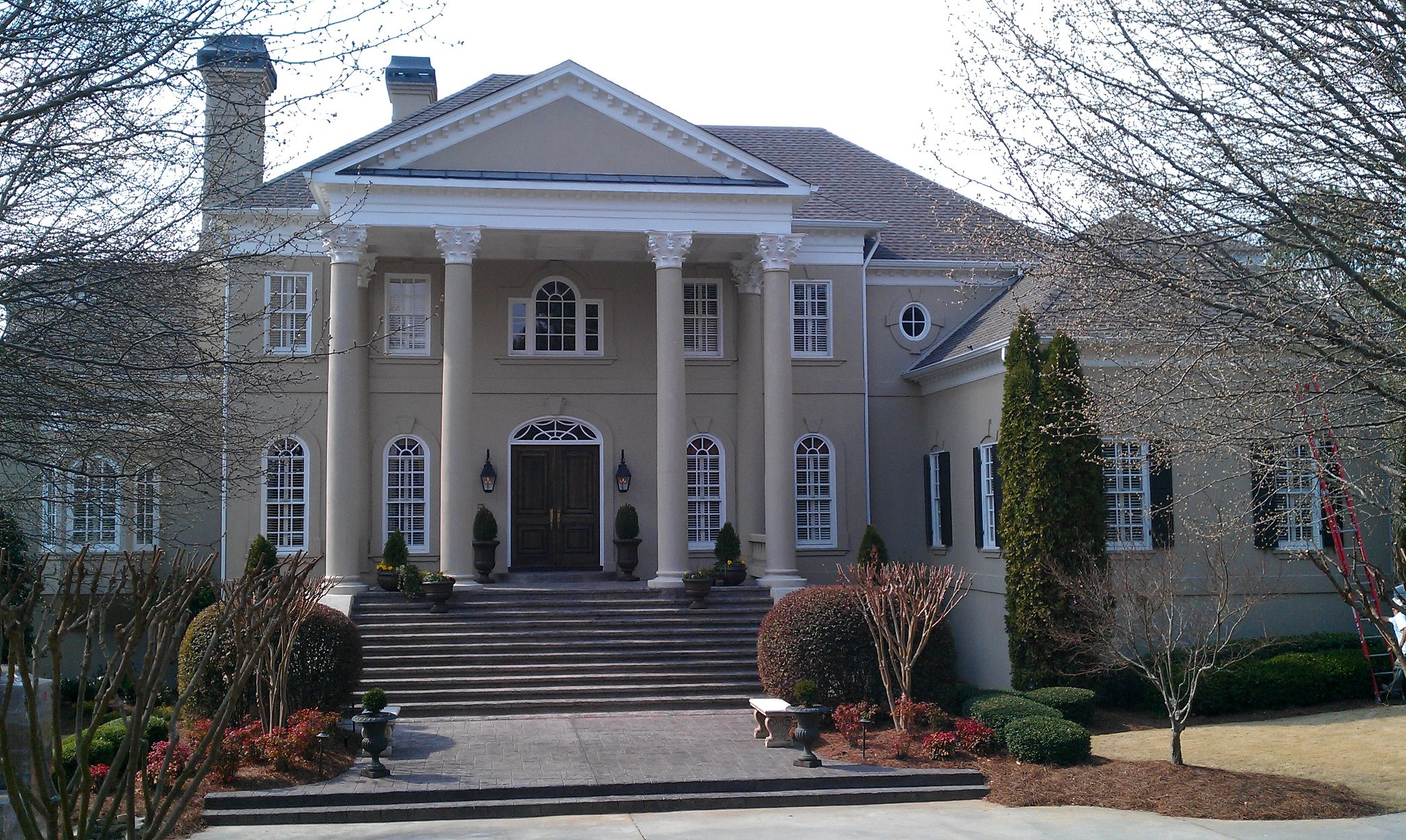
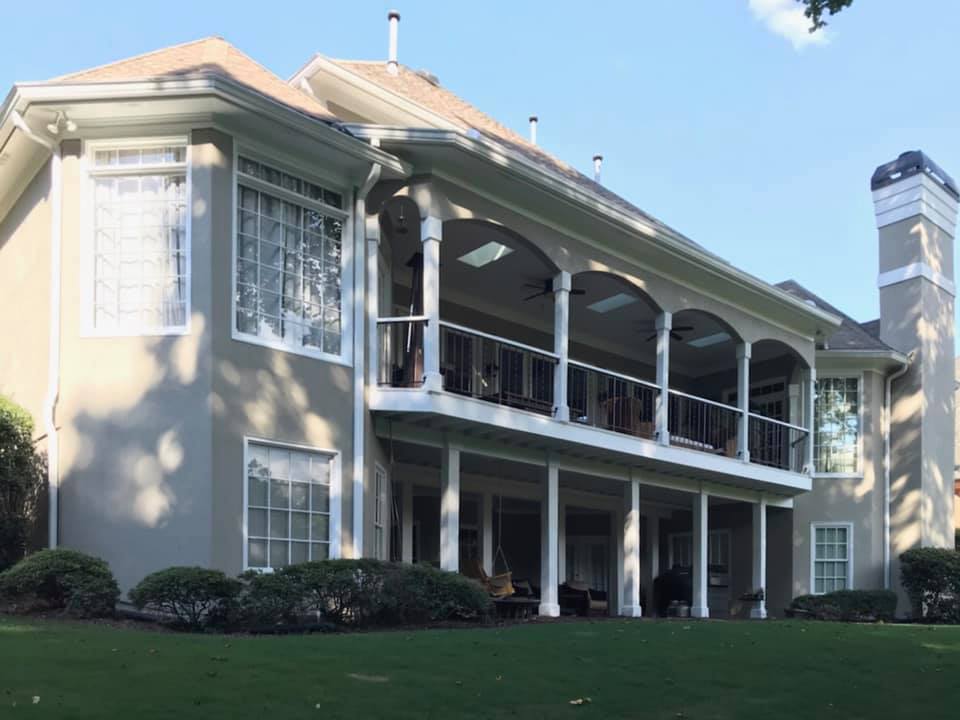
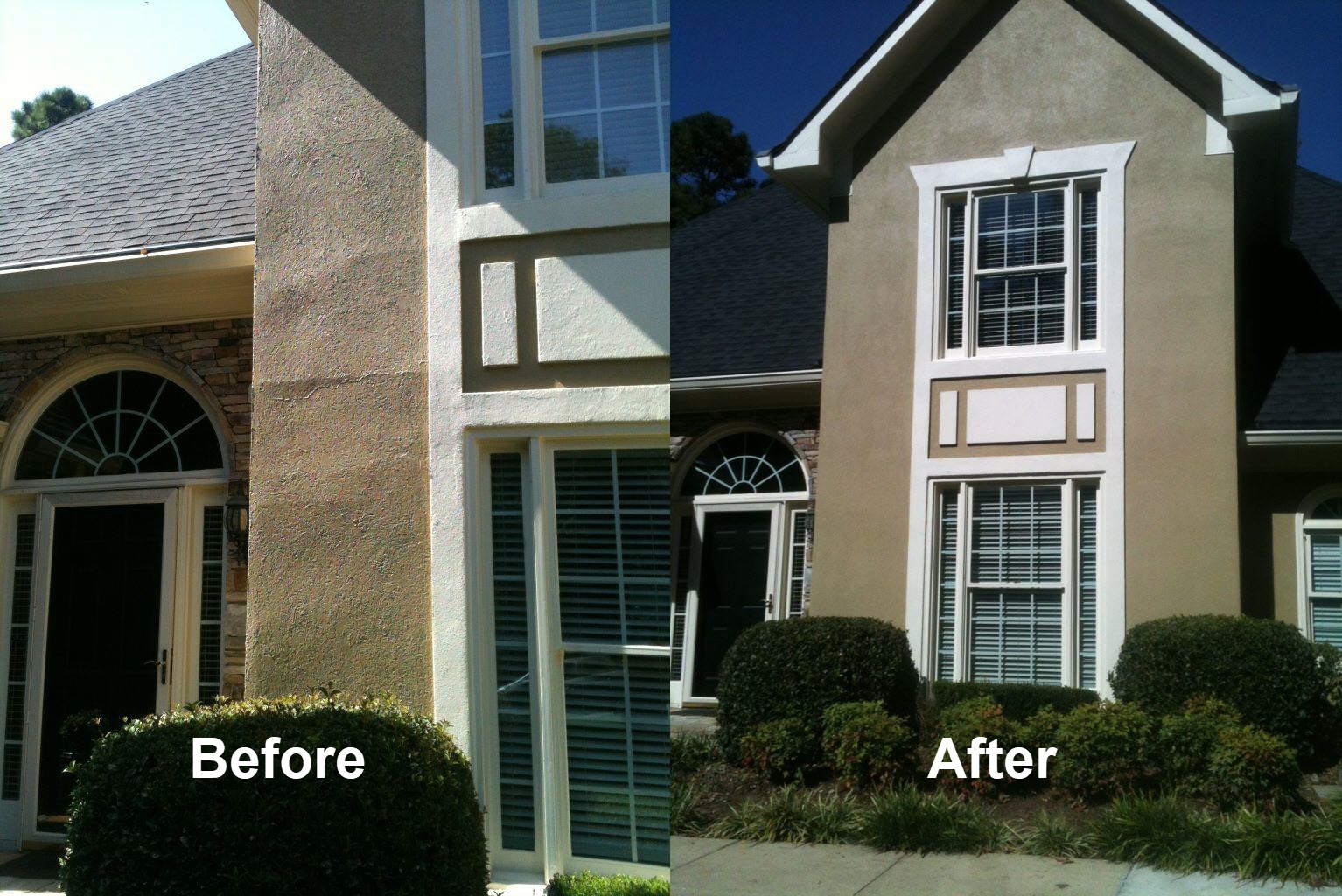
Call Us Today to receive your Free Quote for
Carpentry in Woodstock
Serving: Woodstock, Georgia
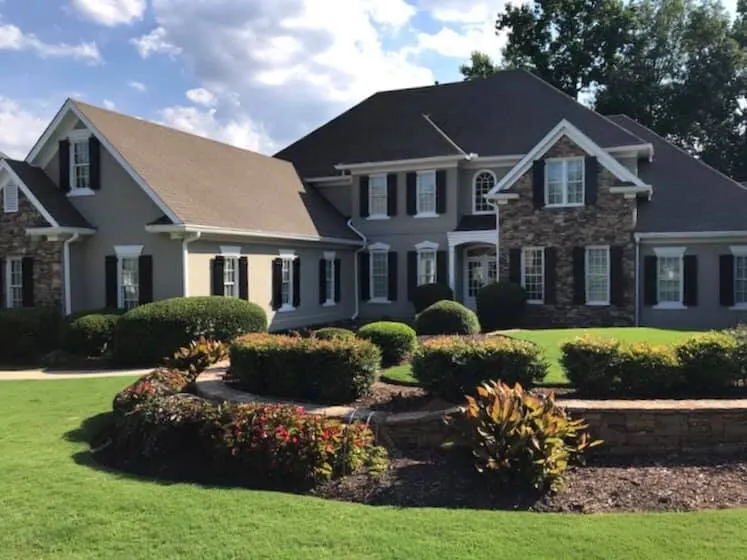
About Woodstock, Georgia
Native Americans were removed from the area.
The Georgia General Assembly incorporated Woodstock as a town in 1897. The community derives its name from Woodstock, an 1826 novel by Walter Scott.
The Woodstock Depot was built in 1912 by the Louisville & Nashville Railroad as the town grew. The line transported cotton, rope, and other agricultural products, as well as passengers. Passenger service ended in 1949.
According to the United States Census Bureau, Woodstock has a total area of 11.3 square miles (29.2Â km), of which 11.2 square miles (28.9Â km) is land and 0.12 square miles (0.3Â km), or 0.92%, is water.
Census | Pop. | Note | %± |
---|---|---|---|
1880 | 92 | — | |
1900 | 276 | — | |
1910 | 442 | 60.1% | |
1920 | 415 | −6.1% | |
1930 | 421 | 1.4% | |
1940 | 389 | −7.6% | |
1950 | 545 | 40.1% | |
1960 | 726 | 33.2% | |
1970 | 870 | 19.8% | |
1980 | 2,699 | 210.2% | |
1990 | 4,361 | 61.6% | |
2000 | 10,050 | 130.5% | |
2010 | 23,896 | 137.8% | |
2020 | 35,065 | 46.7% | |
U.S. Decennial Census |
Race | Num. | Perc. |
---|---|---|
White (non-Hispanic) | 23,727 | 67.67% |
Black or African American (non-Hispanic) | 3,856 | 11.0% |
Native American | 35 | 0.1% |
Asian | 1,529 | 4.36% |
Pacific Islander | 20 | 0.06% |
Other/Mixed | 2,005 | 5.72% |
Hispanic or Latino | 3,893 | 11.1% |
As of the 2020 United States census, there were 35,065 people, 12,878 households, and 8,464 families residing in the city.
As of the census of 2010, there were 23,896 people, 9,580 households, and 6,137 families residing in the city. The population density was 2,715.4 inhabitants per square mile (1,048.4/km). There were 10,298 housing units at an average density of 1,170.2 per square mile (451.8/km). The racial makeup of the city was 79.3% White, 10.2% African American, 0.2% American Indian, 4.5% Asian, 0.02% Pacific Islander, 2.7% from other races, and 3.1% from two or more races. Hispanic or Latino of any race were 9.7% of the population.
There were 9,580 households, out of which 35.2% had children under the age of 18 living with them, 48.8% were married couples living together, 11.7% had a female householder with no husband present, and 35.9% were non-families. Of all households, 29.3% were made up of individuals, and 7.5% had someone living alone who was 65 years of age or older. The average household size was 2.48 and the average family size was 3.12.
In the city, the age distribution of the population shows 26.5% under the age of 18, 6.8% from 18 to 24, 37.4% from 25 to 44, 20.8% from 45 to 64, and 8.5% who were 65 years of age or older. The median age was 34 years. For every 100 females, there were 88.4 males. For every 100 females age 18 and over, there were 84.1 males.
In 2000, the median income for a household in the city was $58,506, and the median income for a family was $65,740. Males had a median income of $48,054 versus $32,798 for females. The per capita income for the city was $25,586. About 2.2% of families and 4.2% of the population were below the poverty line, including 5.0% of those under age 18 and 8.6% of those age 65 or over.
As of the census of 2000, there are 10,050 people, 3,869 households, and 2,627 families residing in the city. The population density is 440.4/km (1,140.4/mi). There are 4,102 housing units at an average density of 179.8 persons/km (465.5 persons/mi). The racial makeup of the city is 89.42% White, 5.05% African American, 0.29% Native American, 1.66% Asian, 0.02% Pacific Islander, 1.94% from other races, and 1.61% from two or more races. 4.94% of the population are Hispanic or Latino of any race.
There are 3,869 households out of which 37.7% have children under the age of 18 living with them, 55.1% are married couples living together, 9.5% have a woman whose husband does not live with her, and 32.1% are non-families. Of all households, 26.1% are made up of individuals and 6.4% have someone living alone who is 65 years of age or older. The average household size is 2.55 and the average family size is 3.10.
In the city the population age distribution is 26.8% under the age of 18, 7.9% from 18 to 24, 39.0% from 25 to 44, 18.3% from 45 to 64, and 8.0% who are 65 years of age or older. The median age is 33 years. For every 100 females there are 92.2 males. For every 100 females age 18 and over, there are 87.4 males.
The median income for a household in the city is $58,506, and the median income for a family is $65,740. Males have a median income of $48,054 versus $32,798 for females. The per capita income for the city is $25,586. 4.2% of the population and 2.2% of families are below the poverty line. Out of the total people living in poverty, 5.0% are under the age of 18 and 8.6% are 65 or older.