Plaster Wallsin Decatur GA
Plaster Walls That Combine Tradition and Modern Craftsmanship
We Are Locally Owned & Operated For Over 24 Years
We Serve Businesses In And Around The Following Cities:
About Plaster Walls in Decatur, Georgia
Understanding and Mastering Plaster Walls for Effective Stucco, EIFS, and Dryvit Installations in Decatur, Georgia
Setting the Foundation for Plaster Walls in Decatur
Decatur, Georgia, with its blend of historic charm and modern elegance, stands as a testament to varied architectural styles. The use of plaster walls in both residential and commercial properties is a reflection of both tradition and innovation. Whether it's the timeless allure of venetian plaster walls or the practicality of textured plaster walls, these surfaces provide aesthetics and durability that are hard to match. In this vibrant city, the need for quality installation and repair services for such plastered structures has never been more crucial. Advanced Stucco Repair offers expertise in handling all aspects of plastering, including the installation of Stucco, Exterior Insulation and Finish System (EIFS), and Dryvit. The importance of such expertise cannot be understated, as it guarantees that the charm of Decatur's buildings is preserved and enhanced.
The Art of Plaster Wall Installation
Plaster wall installation is both a science and an art form. It requires a deep understanding of materials, techniques, and local weather conditions. Plaster, a composite material that combines water, aggregate, and a binder, whether it's the timeless lime plaster walls used historically or the more modern gypsum plaster walls, serves as a protective and aesthetic layer for buildings. When it comes to installing plaster walls, the foundation of the structure plays a critical role. Lath, often composed of thin wooden strips or metal mesh, supports the plaster application, offering strength and stability. The interaction between lath and plaster creates a solid surface that acts as a canvas for subsequent finishes and textures.
In Decatur, properties range from historic homes requiring the delicate touch of repairing old plaster walls to commercial properties opting for the modern appeal of lightweight plaster. Advanced Stucco Repair excels in understanding these nuances. Their approach respects the integrity of lath plaster walls while ensuring that finished surfaces meet contemporary expectations of durability and design.
Techniques for Repairing and Fixing Plaster Walls
Over time, even the most meticulously installed plaster walls may require repair. Cracks can develop due to structural changes, moisture, or simply the passage of time. Understanding the nuances of fixing plaster walls is essential, especially when dealing with decorative plaster walls where aesthetics are as important as function.
The process usually begins with identifying the extent and causes of the damage. This might involve repairing plaster walls by filling in cracks with a suitable compound and ensuring a seamless blend with the existing surface. Advanced Stucco Repair utilizes techniques such as skim coating plaster walls to renew surfaces effectively, ensuring a smooth, consistent finish. When dealing with historical structures, this might involve replicating intricate designs, preserving both the history and value of the property.
The Versatility of Stucco and EIFS Systems
Stucco, an exterior plaster finish, offers a blend of aesthetics and functionality that has been appreciated for centuries. It's known for its durability, resistance to weather, and ability to provide a visually appealing exterior. Stucco's adaptability makes it suitable for various surfaces, allowing for creative expressions ranging from smooth to textured finishes.
On the other hand, EIFS provides a more modern solution with its insulation benefits. It comprises several layers, including insulation boards and a synthetic finish. This intricate system contributes not only to the beauty of a building but also to energy efficiency. Dryvit, a leading brand in EIFS, offers solutions that merge the aesthetic possibilities of plaster exterior walls with modern demands for efficiency and sustainability.
Having skilled professionals like Advanced Stucco Repair handle these installations ensures that both the aesthetic and functional potential of these systems are fully realized. Their in-depth knowledge allows them to select and apply the right materials and techniques for each specific project, ensuring optimum results every time.
Case Studies and Real-World Applications
The application of plaster walls, stucco, EIFS, and Dryvit in Decatur's real estate is both varied and impressive. Consider a residential property with old plaster walls that require not just restoration but transformation. Through meticulous repair and refinishing, a home can be reinvented without losing its historic charm. A decorative plaster wall installation might be implemented to enhance the elegance of an interior space.
In the commercial sector, businesses often seek the cost-saving energy benefits of EIFS. Aided by Advanced Stucco Repair's expertise, many buildings have undergone transformations that reduce energy costs while enhancing exterior aesthetics. These case studies exemplify how businesses not only enhance their property value but also improve functionality and energy efficiency through the correct application of plaster technologies.
The Benefits of Choosing Advanced Stucco Repair
Opting for expert services is imperative when dealing with complex installations and repairs of plaster systems like Stucco, EIFS, and Dryvit. Advanced Stucco Repair offers invaluable expertise that ensures each project's success. With their commitment to quality, they provide solutions that stand the test of time and transform residential and commercial properties throughout Decatur.
Working with skilled professionals means problems such as moisture infiltration or inadequate adhesion can be effectively managed. Their understanding of the local climate and architecture allows for solutions that are not only effective but harmonious with Decatur's architectural landscape. This is an assurance that whether you're repairing old plaster walls or installing new stucco finishes, the results will be both functional and visually satisfying.
Transforming Spaces with Plaster Wall Innovations
The evolution of plaster applications continues to offer exciting possibilities for property owners. Innovative materials and techniques allow for greater creativity and performance. Textured plaster walls, for instance, provide endless design possibilities while aligning with contemporary interior and exterior design trends.
The commitment to innovation that firms like Advanced Stucco Repair maintain means that they're always at the forefront of such developments, bringing the latest techniques and materials to their clients in Decatur. This results in homes and businesses that not only meet but exceed modern expectations for durability and aesthetics.
For those in Decatur looking to enhance their property with plaster wall solutions, partnering with an expert like Advanced Stucco Repair makes all the difference. It's a collaboration that ensures transformative results, adding true value and aesthetic appeal to any building.
Ultimately, the decision to engage professional services for plaster wall installations and repairs is one that promises quality and longevity. By understanding the intricacies involved, Advanced Stucco Repair guides their clients through the process, offering personalized services that cater to the unique needs of each project. This commitment to excellence is what sets them apart, ensuring that Decatur's structures are as beautiful as they are enduring.
Plaster Walls Gallery
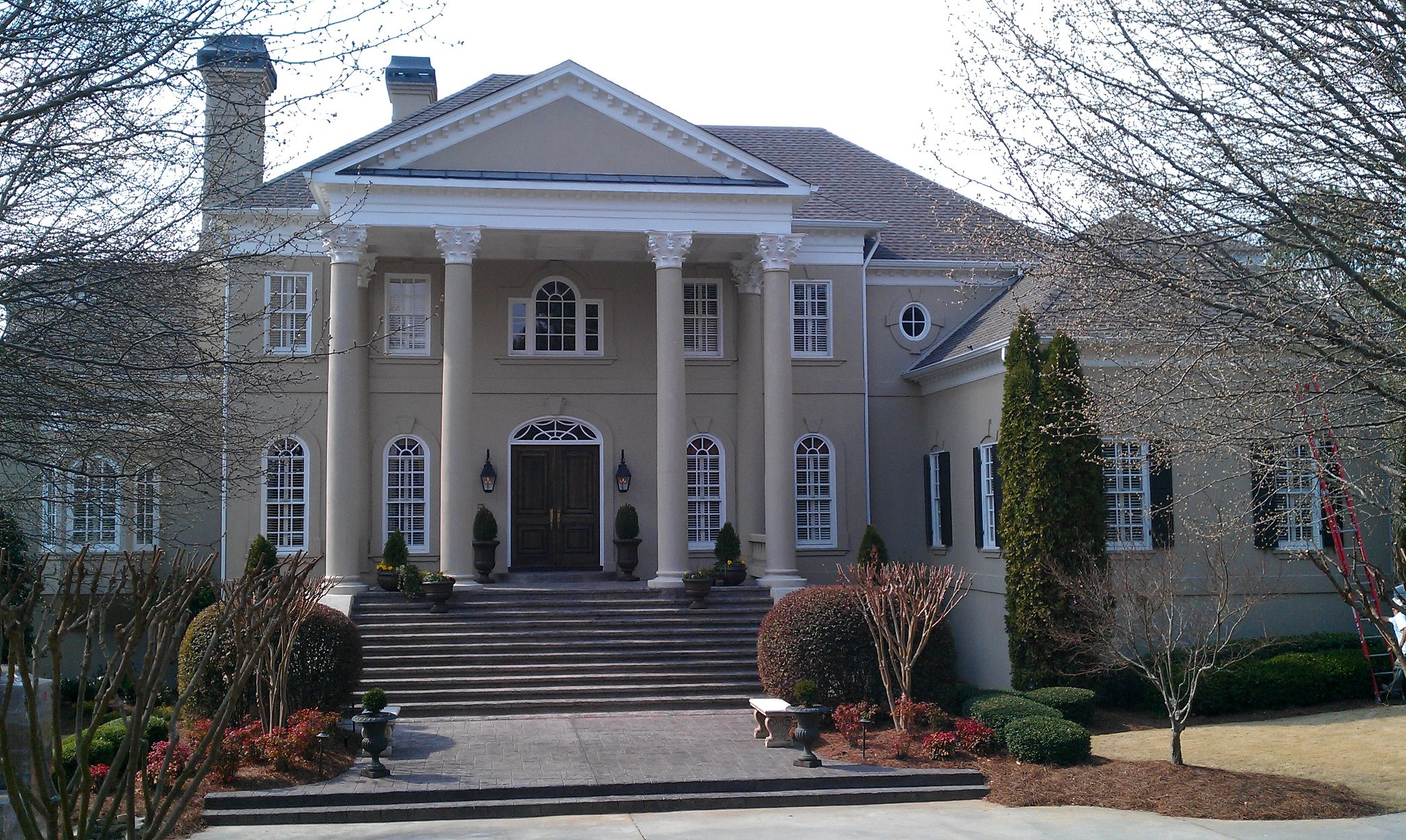
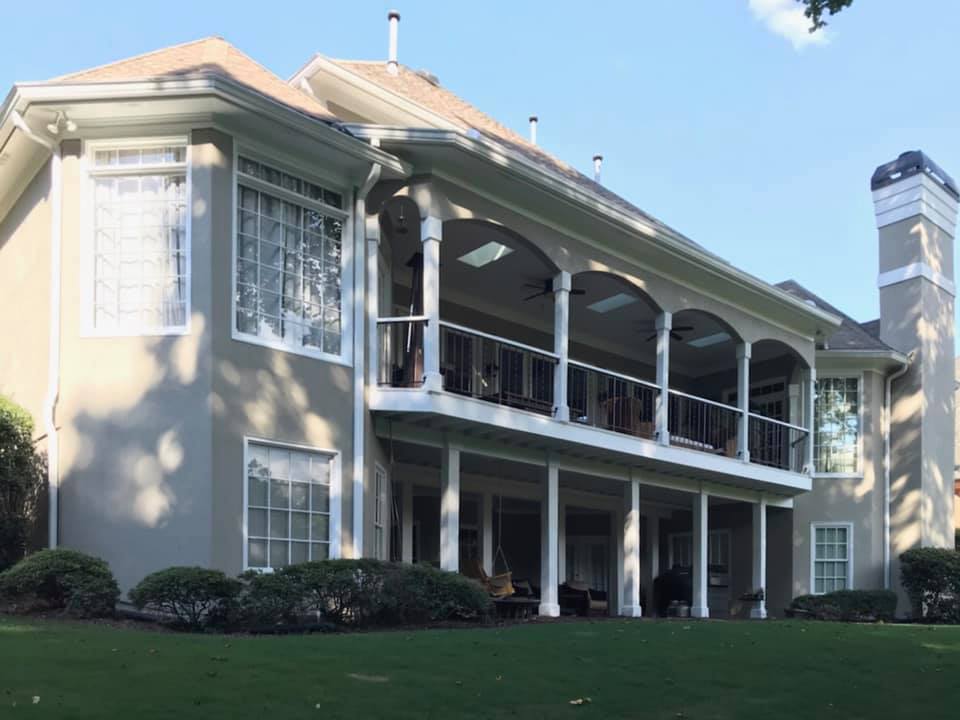
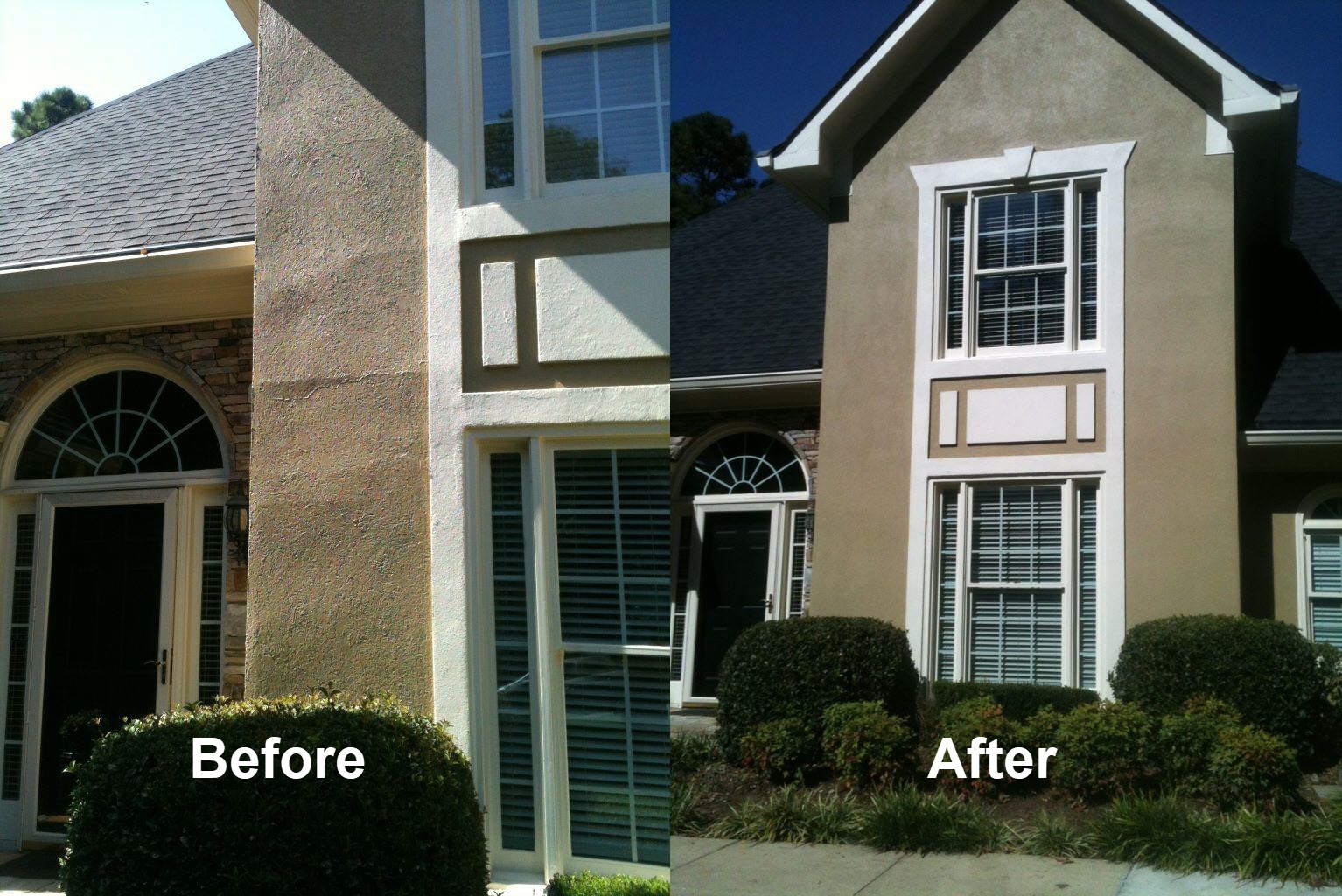
Call Us Today to receive your Free Quote for
Plaster Walls in Decatur
Serving: Decatur, Georgia
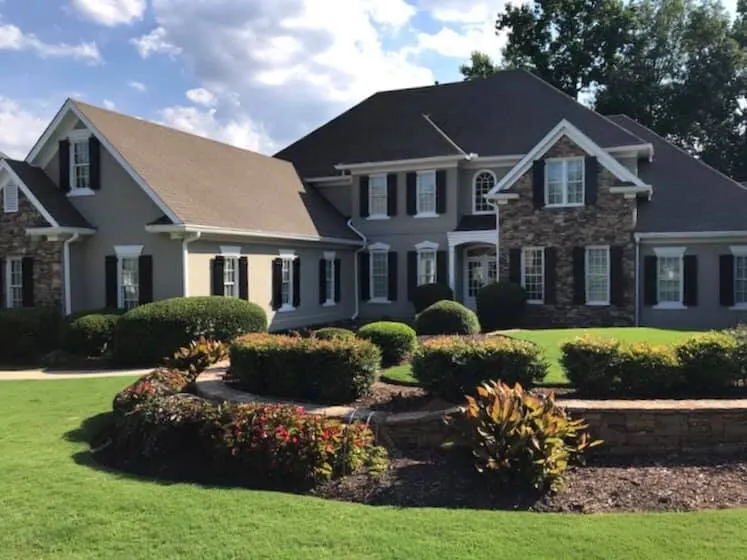
About Decatur, Georgia
Prior to European settlement, the Decatur area was largely forested (a remnant of old-growth forest near Decatur is preserved as Fernbank Forest). Decatur was established at the intersection of two Native American trails: the Sandtown, which led east from the Chattahoochee River at Utoy Creek, and the Shallowford, which follows today's Clairmont Road, and eventually crossed near Roswell. A site for the DeKalb County courthouse was designated in 1822 in what would become downtown Decatur; the city of Decatur was incorporated on December 10, 1823. It was named for United States Navy Commodore Stephen Decatur.
The first settler in the area were farmers or skilled tradesmen of English, Scottish and Irish descent.
During the American Civil War, Decatur became a strategic site in Sherman's Atlanta Campaign. In July 1864, Major-General James McPherson occupied the town to cut off the Confederates' supply line from Augusta. On July 22, during the Battle of Atlanta, Confederate cavalry under Major-General Joseph Wheeler attacked McPherson's supply wagons and the Union troops left to defend the wagons. A historical marker at the old courthouse marks the site of this skirmish.
In the second half of the twentieth century the metropolitan area of Atlanta expanded into unincorporated DeKalb County, eventually surrounding two sides of the town of Decatur. Concurrently, the area experienced white flight, as many residents fled to more distant suburbs. The 1960s and 1970s witnessed dramatic drops in property values. However, more recently the city has regained economic vigor, partially thanks to several long-term downtown development plans that have come to fruition, making Decatur a trendy small mixed-use district with easy transit to downtown Atlanta. Over the past twenty years, it has gained a local and national reputation as a progressive city with a high level of citizen involvement.
According to the United States Census Bureau, the city has a total area of 4.2 square miles (11 square kilometers), all land. Decatur is bordered by Avondale Estates to the southeast and Atlanta to the southwest, and unincorporated DeKalb County elsewhere.
The Eastern Continental Divide bisects the city along the CSX (formerly Georgia Railroad) trackage right of way.
Census | Pop. | Note | %± |
---|---|---|---|
1840 | 530 | — | |
1850 | 744 | 40.4% | |
1870 | 401 | — | |
1880 | 639 | 59.4% | |
1890 | 1,013 | 58.5% | |
1900 | 1,418 | 40.0% | |
1910 | 2,466 | 73.9% | |
1920 | 6,150 | 149.4% | |
1930 | 13,276 | 115.9% | |
1940 | 16,561 | 24.7% | |
1950 | 21,635 | 30.6% | |
1960 | 22,026 | 1.8% | |
1970 | 21,943 | −0.4% | |
1980 | 18,404 | −16.1% | |
1990 | 17,304 | −6.0% | |
2000 | 18,147 | 4.9% | |
2010 | 19,335 | 6.5% | |
2020 | 24,928 | 28.9% | |
U.S. Decennial Census 2010–2020 |
Race | Num. | Perc. |
---|---|---|
White (non-Hispanic) | 16,796 | 67.38% |
Black or African American (non-Hispanic) | 3,839 | 15.4% |
Native American | 36 | 0.14% |
Asian | 1,317 | 5.28% |
Pacific Islander | 12 | 0.05% |
Other/Mixed | 1,634 | 6.55% |
Hispanic or Latino | 1,294 | 5.19% |
As of the 2020 United States census, there were 24,928 people, 8,841 households, and 5,597 families residing in the city.
Decatur has operated under a Commission-Manager form of government since 1920. The Charter of the City of Decatur establishes the City Commission as the governing and legislative authority of the City government. A five-member City Commission is elected for four-year terms on two-year cycles. Two members are elected from the south side of the city, two from the north side and one is elected at-large. At their organizational meeting each January, the Commissioners elect a mayor and mayor-pro-tem from among their own membership for a one-year term. The mayor is not a separate elected office. The current mayor is Patti Garrett. Previous mayors have included Leslie Jasper Steele (1915), Jack Hamilton, Walter Drake, Mike Mears, Ann A. Crichton, Elizabeth Wilson, William Floyd, Jim Baskett and Scott Candler, Sr. (known as Mr. DeKalb).
The Commission appoints a professional City Manager to carry out the policies, directives and day-to-day business of the city. The current city manager is Andrea Arnold. There are also several citizen volunteer boards and commissions appointed by the City Commission, including the Planning Commission, the Zoning Board of Appeals, and the Historic Preservation Commission.
The Georgia Department of Juvenile Justice has its headquarters in Avondale Estates, near Decatur. The Georgia Bureau of Investigation has its headquarters near Decatur, in an unincorporated area.
The United States Postal Service operates the Decatur Post Office.
City Schools of Decatur, which serves only students within the city limits, holds pre-school to grade twelve, and consists of a pre-K early childhood learning center, five lower elementary schools, two upper elementary schools, a middle school, and a high school. Decatur High School is the district's sole high school. The Decatur City district has 224 full-time teachers and over 4,400 students from pre-K through grade 12.
The DeKalb County School District serves unincorporated DeKalb County.
The Roman Catholic Archdiocese of Atlanta operates St. Thomas More School in Decatur; it opened on September 1, 1950. At first it only had elementary grades and its initial enrollment was 150. A dedicated elementary building opened in 1955, and an addition for kindergarten classes with two rooms was placed in 1994. St. Peter Claver Regional School has a Decatur mailing address but is in nearby Candler-McAfee CDP.
- Agnes Scott College
- Columbia Theological Seminary
- Georgia State University's Perimeter College
- DeVry University
- Emory University, northwest of Decatur, was located in unincorporated DeKalb County before being annexed by the City of Atlanta in 2017.
The DeKalb County Public Library system operates the Decatur Branch and is also the Dekalb County Library Headquarters.