Stucco Meshin Lilburn GA
Stucco Mesh for Reinforcement and Stability
We Are Locally Owned & Operated For Over 24 Years
We Serve Businesses In And Around The Following Cities:
About Stucco Meshes in Lilburn, Georgia
The Role of Stucco Mesh in Lasting Exterior Finishes in Lilburn
In Lilburn, Georgia, where rapid growth and diverse architectural styles blend historic Southern charm with contemporary design, exterior finishes play a vital role in preserving the durability and appearance of homes and commercial buildings. Among the many components of an exterior cladding system, one that often goes unnoticed yet provides essential structural support is the stucco mesh. This unassuming layer embedded beneath the stucco finish ensures strength, flexibility, and endurance of the wall covering over time—an indispensable part of any quality stucco system, particularly vital for the humid subtropical climate of Gwinnett County.
Whether you're building a new home, managing a commercial renovation, or addressing weather-related repairs, understanding the correct integration of materials like stucco mesh is critical. Products such as EIFS (Exterior Insulation and Finish Systems) and synthetic stucco like Dryvit rely heavily on proper mesh installation for their performance. When improperly installed or neglected, stucco finishes can crack, bulge, or entirely separate from the structure, leading to costly repairs and even structural concerns. That's where local specialists such as Advanced Stucco Repair serve as a valuable resource for residents and business owners alike, ensuring projects are handled with precision from start to finish.
Essential Functions and Material Types
At the heart of any stucco system lies a framework that reinforces and provides the base layer with critical support. Stucco mesh, also known as stucco wire mesh or fiber mesh for stucco depending on the material, is integral to ensuring this support. Typically, these meshes are installed between the base wall and the outer stucco layers. Their purpose is two-fold: first, to allow the stucco to grip and adhere uniformly, and second, to help distribute stresses across the wall, preventing the hairline cracks and larger fissures that can develop over time due to shifting foundations, thermal expansion, or weather-induced movement.
Traditional stucco mesh options include galvanized steel lath, which serves as both a mechanical and bonding platform. More modern installations, such as those used in EIFS systems, include fiberglass or plastic-based mesh materials. These are lightweight, resistant to corrosion, and offer unmatched compatibility with synthetic finishes. Fiber mesh for stucco, in particular, finds favor in both residential renovations and commercial developments throughout Lilburn, especially where Dryvit systems are preferred for their aesthetic and insulating qualities. Regardless of the form, the presence of an effective mesh layer significantly improves the lifespan of the final exterior finish.
Application Process and Best Practices
Proper installation begins with preparation. For exterior walls in Lilburn properties, especially older residences undergoing stucco repair, removing the damaged finish is often the first step. Inspection of the substrate beneath is essential to determine the health of the structure and readiness for new application. Where moisture damage or mold is a concern—a common occurrence in Georgia's humid seasons—remediation precedes mesh layering.
Once prep work is complete, the appropriate stucco mesh is affixed securely to the wall. For three-coat stucco systems, a metal stucco wire mesh is anchored to wood or metal framing using fasteners and wrapped tightly so that it covers corners and edges smoothly. In commercial applications, where fire code and impact resistance are crucial, double layers of mesh are often used to increase durability. In EIFS systems, the process differs slightly—mesh is embedded directly into a base coat that is troweled onto insulation boards, typically made of expanded polystyrene. This embedding process ensures a seamless transition between the supporting layers and the decorative finish, preventing delamination and impact damage.
The base coat and mesh then receive additional finishing layers, ranging from smooth acrylic to textured mineral finishes. The entire process, when handled by experienced professionals like those at Advanced Stucco Repair, takes into account weather conditions, building codes, and localized architectural styles. Experts proficient in Georgia construction nuances ensure that the stucco mesh is not just properly installed, but optimized for long-term resilience.
Why Stucco Mesh Matters in Lilburn Builds
Throughout Lilburn, the urban-rural blend of neighborhoods—ranging from historical homes in the Old Town area to modern commercial plazas along Lawrenceville Highway—requires varied exterior solutions. Traditional stucco continues to be a favored finish due to its timeless appearance and resistance to fire, rot, and pests. But without a well-installed stucco wire mesh or fiber mesh for stucco beneath the surface, even the best-looking stucco finish is vulnerable to structural issues.
Climate is one major factor that proves the worth of proper stucco reinforcement. In the spring and summer months, heavy rains and strong humidity levels can penetrate faulty or poorly meshed stucco systems. This intrusion leads to mold growth behind the stucco and degradation of wooden or foam substrates. Conversely, during winter freezes, moisture trapped within cracked stucco can expand, leading to further cracking and surface separation.
With these climate demands, it’s clear that stucco mesh isn’t just a background material—it’s a frontline defense mechanism. That’s why builders and contractors in the Lilburn area depend on companies like Advanced Stucco Repair, who understand that the unseen layers of a project matter just as much as the final appearance. Their experienced teams ensure every component—from flashing and moisture barriers to the mesh and topcoat—is installed following best practices to prevent future issues.
When to Repair and How to Choose the Right Method
For homeowners and property managers, knowing when a stucco or EIFS system needs attention can save thousands in eventual repair costs. Cracks wider than 1/16 of an inch may indicate movement beneath the surface, while bulging or flaking typically signifies detachment from the underlying mesh. Also, discolored or soft spots may signal moisture intrusion behind the surface, a common issue in older installations lacking modern fiber mesh for stucco.
In residential cases where expansion and contraction due to HVAC use or settling is an issue, reinforcement using a new layer of fiberglass mesh embedded into a fresh base coat may suffice. For commercial blocks prone to physical damage—such as those near parking garages or loading docks—a higher-weight stucco wire mesh layer provides impact resistance and adds safety. Fortunately, companies such as Advanced Stucco Repair offer detailed evaluation before repairs, allowing clients to understand the scope and solutions customized to their structure type and location.
More extensive damage often warrants a full stucco system replacement, particularly when insulation boards behind Dryvit systems have deteriorated due to water intrusion. In these cases, professionals will remove the compromised material, inspect framing and sheathing, and rebuild using new insulation, vapor barriers, and stucco mesh layers engineered for Georgia’s diverse climate landscape.
Integration with Energy Efficiency and Building Codes
One often overlooked advantage of modern stucco mesh, especially when used in EIFS packages, is its compatibility with energy-efficient designs. In Lilburn, a growing number of homeowners and developers are targeting reduced energy consumption while maintaining quality aesthetics. EIFS installations enriched with insulation and fiber mesh for stucco offer high R-values, meaning they better resist heat transfer across the wall system. The mesh not only strengthens the finish but ensures the insulation layer stays undisturbed over time, preserving its thermal properties.
Additionally, meeting wind-load requirements and regional building codes is non-negotiable in Georgia, particularly for commercial properties. The strength-to-weight ratio offered by well-installed stucco mesh allows structures to pass wind resistance standards while keeping project costs reasonable. The flexible nature of fiberglass mesh also allows for creative architectural detailing, commonly seen in schools, churches, and office buildings where contours and depth add character.
A well-versed provider like Advanced Stucco Repair stays abreast of evolving regional codes, helping clients not only avoid penalties but also benefit from energy-based tax incentives associated with high-performance cladding systems. Their history of working in Lilburn ensures compliance and excellence from permitting to final inspections.
Benefits Beyond Durability
While extended lifespan and resilience are the most cited benefits of incorporating stucco mesh, other perks abound. The seamless appearance it facilitates adds real property value, as the wall finish doesn't suffer from rippling or uneven textures. Mesh also allows for quicker repairs in future years—trained technicians can key into the system’s basecoat faster and apply matching material without excessive demolition.
In community settings like condominiums, mesh provides uniformity across various structures, ensuring that facade renovations look cohesive and professional. For restaurants and retail outlets in Lilburn aiming to create a polished storefront, Dryvit systems built with energy-efficient base materials and reinforced fiber mesh produce a façade that looks clean and inviting year-round. Such outcomes translate directly into improved branding and increased customer appeal.
By choosing a local expert like Advanced Stucco Repair, businesses and homeowners alike access tools and craftsmanship that make these benefits achievable. From new developments to government buildings, their approach to mesh installation includes supervisory detail that saves on maintenance later—and that’s an often-unseen benefit worth accounting for.
Local Relevance in a Growing Community
The continued development of Lilburn and its surrounding areas means both new construction and remodeling projects are on the rise. As aging neighborhoods are revitalized and commercial zones expand, stucco continues to rank among the top choices for exteriors due to its customizability. In this increasingly competitive market, properly installed stucco mesh plays a deciding role in the longevity and curb appeal of properties.
For instance, schools upgrading their façades after several decades of service often discover foundational cracks and delaminated surfaces. Expert installers often resolve these challenges through retrofit mesh systems. Using techniques such as layering additional mesh into base coats or replacing entire wall sections, companies like Advanced Stucco Repair not only stop existing issues but extend the life of the exterior for decades to come.
Historic homes in Lilburn, many built with traditional stucco but lacking modern reinforcements, likewise benefit from mesh insertion techniques that allow for gentle restoration without affecting the original aesthetics. Where cathedral-like churches or intricate townhome complexes are involved, mesh selection and placement must be adjusted for species of finish and design complexity, another area where a tailored approach proves most effective.
The demand for these skill sets will only grow as property owners balance modernization with sustainability. Thankfully, trusted contractors with advanced understanding of regional climate and building practices are readily available, smoothing this transition for all types of buildings in Lilburn.
In sum, the role of stucco mesh in building durability, whether through traditional lath or fiber mesh for stucco in modern EIFS, cannot be overstated. It provides the unseen strength beneath the beauty of a well-finished wall, prevents structural vulnerabilities, and contributes to energy savings. Whether you’re upgrading an older façade, building from scratch, or addressing water-related damages, turning to experienced professionals makes all the difference. With a deep knowledge of local conditions and best materials, Advanced Stucco Repair continues to serve as a dependable ally for residential and commercial stucco needs across Lilburn. Their comprehensive process ensures that every layer—especially the one you don’t see—is built to last.
Stucco Meshes Gallery
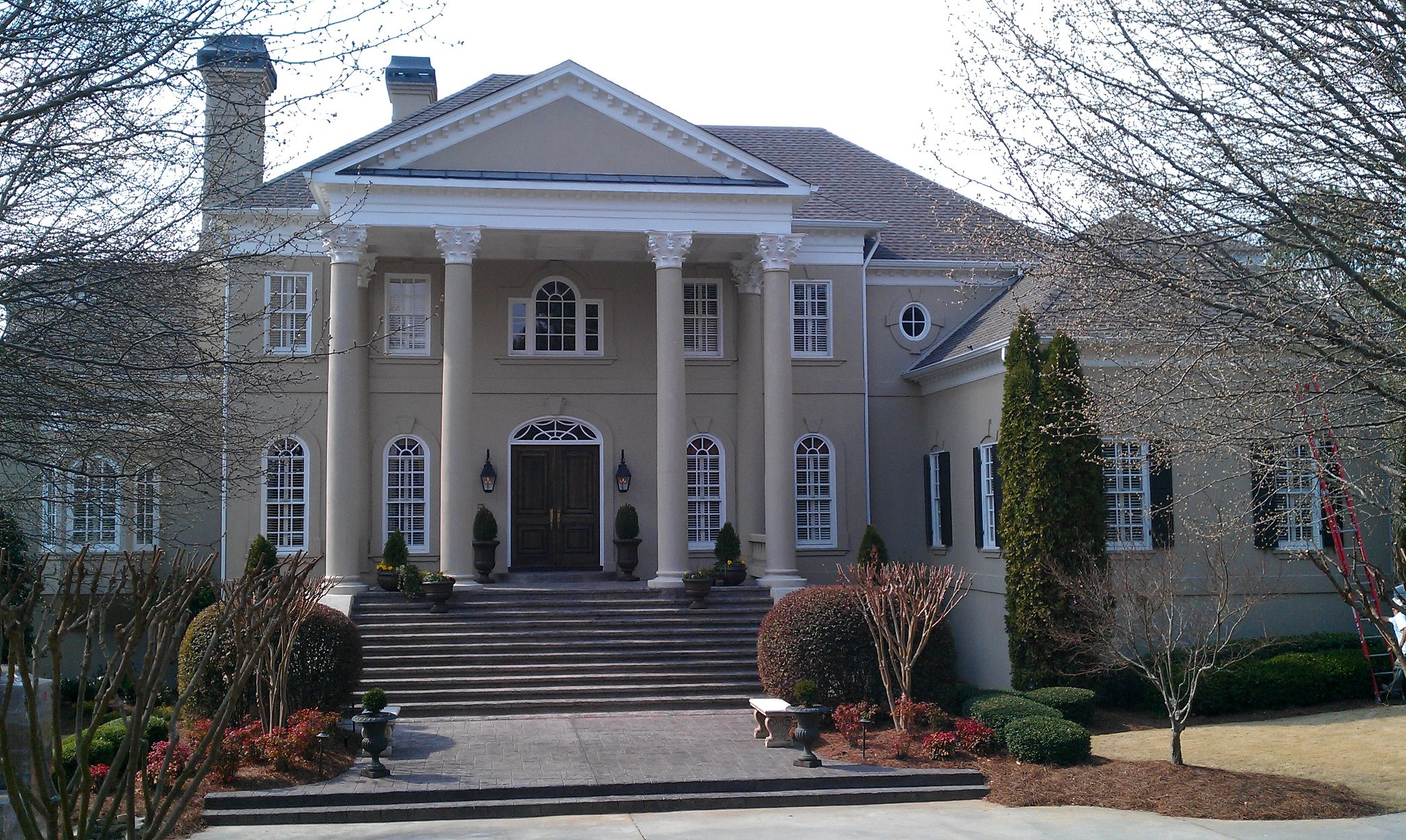
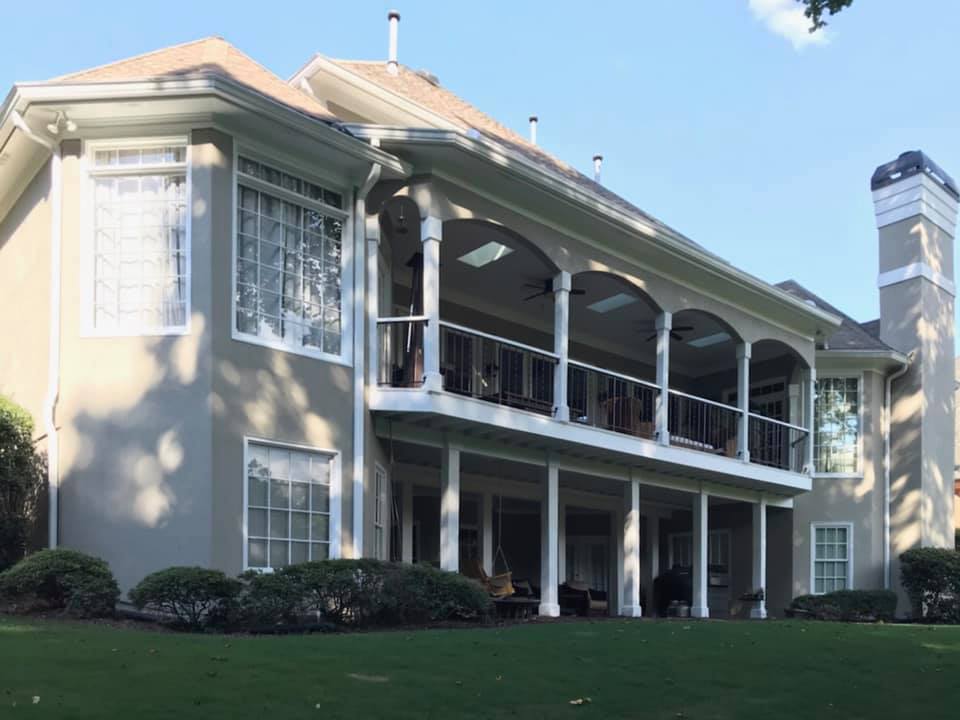
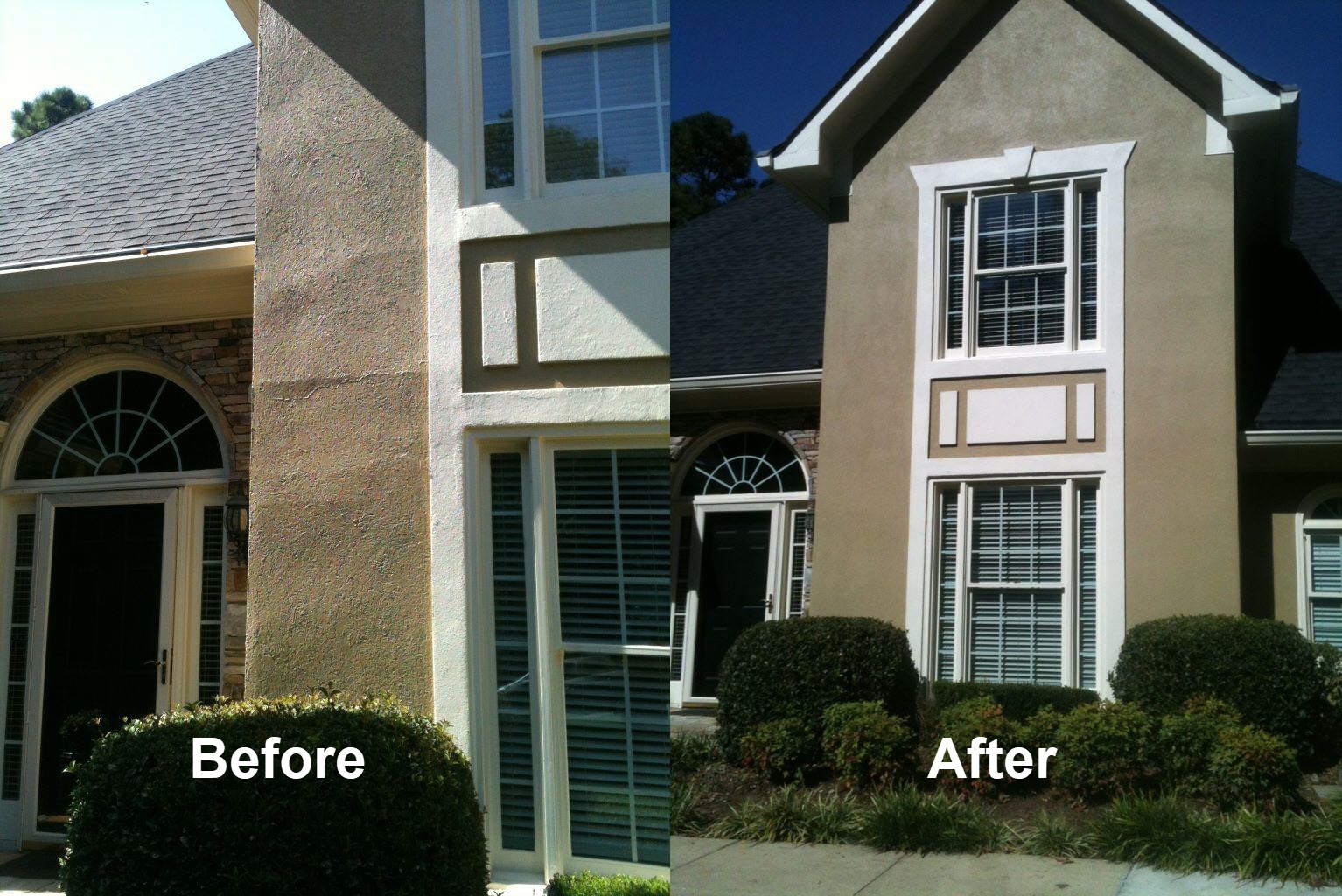
Call Us Today to receive your Free Quote for
Stucco Mesh in Lilburn
Serving: Lilburn, Georgia
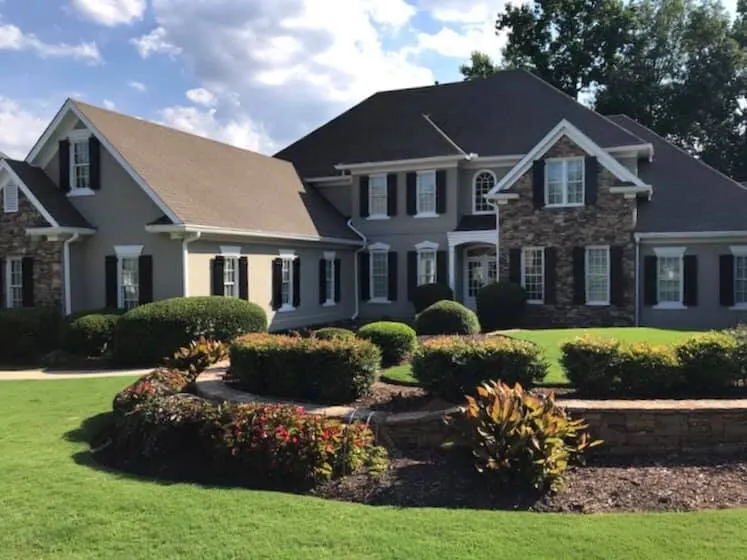
About Lilburn, Georgia
The city of Lilburn was founded in 1890 by the Seaboard Air Line Railway. The area previously known as "McDaniel" was renamed "Lilburn" after the general superintendent of the railroad, Lilburn Trigg Myers of Virginia. The town was incorporated as Lilburn on July 27, 1910.
A devastating fire and hard economic times in the 1920s ended the prosperity. A revitalization of the original historic area has emerged with shopping and restaurants in the Old Town district which has been described as a "slice of history."
Lilburn is located in western Gwinnett County at 33°53′20″N 84°8′27″W / 33.88889°N 84.14083°W (33.888853, -84.140897). U.S. Route 29 (Lawrenceville Highway) passes through the center of town, leading southwest 19 miles (31 km) to downtown Atlanta and northeast 11 miles (18 km) to Lawrenceville, the Gwinnett County seat.
According to the United States Census Bureau, Lilburn has a total area of 6.4 square miles (16.5Â km), of which 6.3 square miles (16.4Â km) is land and 0.04 square miles (0.1Â km), or 0.82%, is water.
Lilburn's downtown is currently undergoing a revitalization project. The city has already constructed a new city hall/library, having already rerouted Main Street's intersection with US 29. This revitalization includes miles of walking/biking paths referred to as the Greenway Trail and the reconstruction of the historic Prohibition Trail Bridges from the early 1900s.
The BAPS Shri Swaminarayan Mandir Atlanta is located in Lilburn, approximately two miles southwest of the city center. It is the tallest building in the city and was the largest Swaminarayan temple outside of India until the Robbinsville, NJ temple opened in 2014.
Census | Pop. | Note | %± |
---|---|---|---|
1930 | 179 | — | |
1960 | 753 | — | |
1970 | 1,668 | 121.5% | |
1980 | 3,765 | 125.7% | |
1990 | 9,301 | 147.0% | |
2000 | 11,307 | 21.6% | |
2010 | 11,596 | 2.6% | |
2020 | 14,502 | 25.1% | |
U.S. Decennial Census |
Race | Num. | Perc. |
---|---|---|
White (non-Hispanic) | 3,613 | 24.91% |
Black or African American (non-Hispanic) | 2,413 | 16.64% |
Native American | 25 | 0.17% |
Asian | 2,882 | 19.87% |
Pacific Islander | 6 | 0.04% |
Other/Mixed | 541 | 3.73% |
Hispanic or Latino | 5,022 | 34.63% |
As of the 2020 United States census, there were 14,502 people, 3,807 households, and 2,873 families residing in the city.
Gwinnett County Public Schools operates public schools.
The following have Lilburn addresses:
Elementary schools
- Arcado Elementary (Parkview)
- Camp Creek Elementary (Parkview)
- G.H. Hopkins Elementary (Meadowcreek)
- Knight Elementary (Parkview)
- Lilburn Elementary (Meadowcreek)
- Mountain Park Elementary (Parkview)
- R.D. Head Elementary (Brookwood)
- Rebecca Minor Elementary (Berkmar)
Middle schools
- Berkmar Middle School (Berkmar)
- Five Forks Middle School (Brookwood)
- Lilburn Middle School (Meadowcreek)
- Trickum Middle School (Parkview)
High schools
- Berkmar High School (Berkmar) - Lilburn
- Brookwood High School (Brookwood) - Snellville
- McClure Health Science High School (Meadowcreek) - Duluth
- Meadowcreek High School (Meadowcreek) - Norcross
- Parkview High School (Parkview) - Lilburn
- Gwinnett College
- Killian Hill Christian School
- Parkview Christian School
- Providence Christian Academy
- Regina Caeli Academy
- St. John Neumann Regional Catholic School
Gwinnett County Public Library operates the Mountain Park Branch and the Lilburn Branch.