Expansion Jointsin Woodstock GA
Tailored Solutions for Long-Lasting Structural Integrity
We Are Locally Owned & Operated For Over 24 Years
We Serve Businesses In And Around The Following Cities:
About Expansion Joints in Woodstock, Georgia
Expansion Joints in Stucco, EIFS, and Dryvit Installation and Repair in Woodstock, Georgia
The Role of Expansion Joints in Building Systems
As the architectural landscape of Woodstock, Georgia evolves, the critical components behind the durable and aesthetically pleasing structures often get overlooked. Among these components, expansion joints stand out as vital elements that provide both functionality and longevity to building exteriors such as stucco, Exterior Insulation and Finish Systems (EIFS), and Dryvit. These materials are known for their versatility and insulation properties, making them popular choices for both residential and commercial properties in the region. In climates like Woodstock’s, characterized by significant temperature fluctuations, the role of expansion joints becomes even more crucial.
Expansion joints are strategically placed gaps that allow for the structural movement caused by temperature changes, moisture variations, and other environmental forces. Without them, the buildings would be prone to cracks and subsequent damage, jeopardizing their structural integrity. They are incorporated to absorb the stresses that temperature changes induce on materials like stucco and EIFS, ensuring that the materials do not buckle or crack under pressure.
Understanding the Different Types of Expansion Joints
The incorporation of expansion joints in construction is not a one-size-fits-all process. Various expansion joints can be utilized depending on the specific needs and characteristics of a structure. In Woodstock, where construction ranges from historical restorations to modern skyscrapers, understanding these distinctions is essential.
Commonly, stucco expansion joints are utilized because of their compatibility with the material’s rigidity and need for movement flexibility. Similarly, EIFS benefits from the precise placement of inbuilt expansion joints, allowing for its otherwise brittle nature to withstand significant environmental stressors. Often, peripheral components like rubber expansion joints complement these systems, providing additional flexibility. They're commonly seen in sidewalks or as brick expansion joints in masonry work around Woodstock's historical areas.
Technological advancements have introduced novel solutions, such as emseal and inpro expansion joints, which offer enhanced sealing properties and greater adaptability, crucial for the humid climates of Georgia. Furthermore, conduit expansion joints are essential for installations involving electrical and plumbing conduits, ensuring that the rigid frames don't suffer from joint fractures. Understanding these aspects allows stakeholders to make informed decisions, leading to sustainable building practices.
Applications in Residential and Commercial Properties
Expansion joints hold varied applications across residential and commercial properties in Woodstock. For residential properties, the aesthetic and structural integrity of surfaces like drywall or sheetrock are maintained using drywall expansion joints. In cases where moisture exposure is prevalent, like bathroom or basement settings, fiber expansion joints or PVC expansion joints provide durability against moisture infiltration.
Commercial properties benefit significantly from bellows expansion joints or fabric expansion joints, particularly in buildings with advanced HVAC duct systems. Ductwork expansion joints play an essential role in preventing heat-induced stresses that could otherwise lead to detrimental deformations and costly repairs. Meanwhile, wall expansion joints and floor expansion joints preserve the unyielding strength of commercial infrastructures while keeping maintenance requirements low.
In the heart of Woodstock, areas with parking lots and driveways heavily rely on durable materials that withstand consistent use. Here, asphalt expansion joints or rubber expansion joints absorb substantial vehicular stress, preserving the asphalt’s lifespan. For property owners looking to maintain or replace existing systems, consulting with experts like Advanced Stucco Repair ensures more resilient installations, preventing rapid deterioration.
The Process of Installing Expansion Joints
Installing expansion joints is a detailed process that requires precision and experience. For property owners in Woodstock, leveraging the expertise of specialists such as Advanced Stucco Repair is a prudent choice. Their team ensures thorough inspections before installation to determine the specific needs of the building, taking into account factors such as environmental exposure, building materials, and expected load stresses.
The process begins with a detailed analysis of the areas requiring expansion joints. Upon identifying the required locations, the team employs techniques best suited for the specific building materials involved, whether they be stucco, EIFS, or Dryvit. Using the appropriate expansion joint type ensures the seamless integration of these joints, preserving the architectural integrity while optimizing functionality. Whether employing metal expansion joints in larger commercial buildings or rubber for expansion joints in more elastic settings, the choice is driven by both engineering requirements and aesthetic appeal.
Certain situations call for more specialized applications, such as in proco expansion joints, which are prevalent in high-demand industrial sectors requiring superior stress absorption. This nuanced tailoring is instrumental in aligning a building’s functionality with Woodstock's unique environmental demands.
Maintaining and Repairing Expansion Joints
Just like any other building component, expansion joints in Woodstock require regular maintenance to ensure they function correctly and last long. Especially in a region characterized by moist, warm summers and cold, sometimes icy winters, these joints endure much stress and pollutants. Regular inspections, ideally performed by industry professionals such as Advanced Stucco Repair, can preempt expensive repairs by identifying signs of wear early. Failing to maintain them can lead to issues like water ingress in the case of improperly sealed expansion joints or damage in wall to wall expansion joint systems.
Repairing expansion joints can involve replacing old or damaged components or resealing cracked surfaces. Specific products, like the versatile schluter expansion joint, offer robust solutions that adapt well to both residential and commercial applications. Advanced Stucco Repair’s proficiency in installing and replacing expansion joints ensures that properties retain their structural fortitude and visual appeal, saving property owners future headaches and costs.
In situations where notable defects like leaking or excessive movement are observed, advanced solutions such as metraflex and balco expansion joints might be recommended to meet high durability thresholds. Meanwhile, relocatable sections like sidewalk expansion joints might offer the flexibility needed to accommodate future infrastructure upgrades.
Benefits of Professional Installation and Repair Services
The expert installation and repair of expansion joints offer substantial benefits that go beyond mere compliance with building codes. For Woodstock property owners, choosing a professional service like Advanced Stucco Repair guarantees that every aspect of your property—from condition assessments to product selection and installation—is handled with care, precision, and an eye for long-term sustainability benefits. This approach results not only in enhanced aesthetic appeal and structural integrity but also in reduced maintenance requirements over the building's lifespan.
Moreover, a professionally conducted installation can significantly lower the incidents of sudden failures or costly repairs. For example, employing general rubber expansion joints or wooden expansion joints, when suitable, ensures a robust response to Woodstock’s humidity and temperature extremes. Strong, adaptive joints minimize the risk of building envelope failure, effectively protecting the substantial investment that properties represent.
Professional installers offer the knowledge and experience that crucially guide decisions regarding a building’s unique requirements, aligning them with both present needs and future sustainability. Moreover, working with experienced local professionals, such as those at Advanced Stucco Repair, means you're benefiting from contractors who understand the local climate and construction trends, ensuring tailor-made solutions that stand the test of time.
Real-World Outcomes and Community Impact
Across Woodstock, numerous properties have benefitted greatly from the use of quality expansion joints, courtesy of experts like Advanced Stucco Repair. Real estate developers and homeowners alike can attest to the profound difference these seemingly small components make in terms of durability and property value. For businesses and commercial entities, robust expansion joints spell lower repair costs and uninterrupted operations, factors that directly contribute to business productivity and profitability.
For residents and community members, the visible decrease in wear and tear helps preserve Woodstock’s unique aesthetic and charm, promoting community pride and cohesion. With advanced installations like those seen in outlets and communal areas, safety is noticeably heightened—minimizing the risks of cracks that may pose tripping hazards or look unappealing.
Communities with well-maintained infrastructures perform better economically, attract more investment, and reflect a higher quality of life overall, showcasing the significant impact of quality building practices and well-maintained expansion systems.
In summary, expansion joints play a crucial role in maintaining the structural integrity and aesthetic appeal of Woodstock’s buildings in both residential and commercial settings. Their careful selection, installation, and maintenance ensure that every property can effectively withstand the environmental pressures inflicted by Woodstock’s climate. Opting for expert services from professionals like Advanced Stucco Repair ensures peace of mind and long-term financial benefits, protecting both personal and community investments. These joints, while small in size, carry the weight of significant function and support, driving the sustainable development and preservation of properties in Woodstock, Georgia. For those looking to ensure their properties stand resilient for years to come, now is the opportunity to engage with knowledgeable, trusted partners in the field.
Expansion Joints Gallery
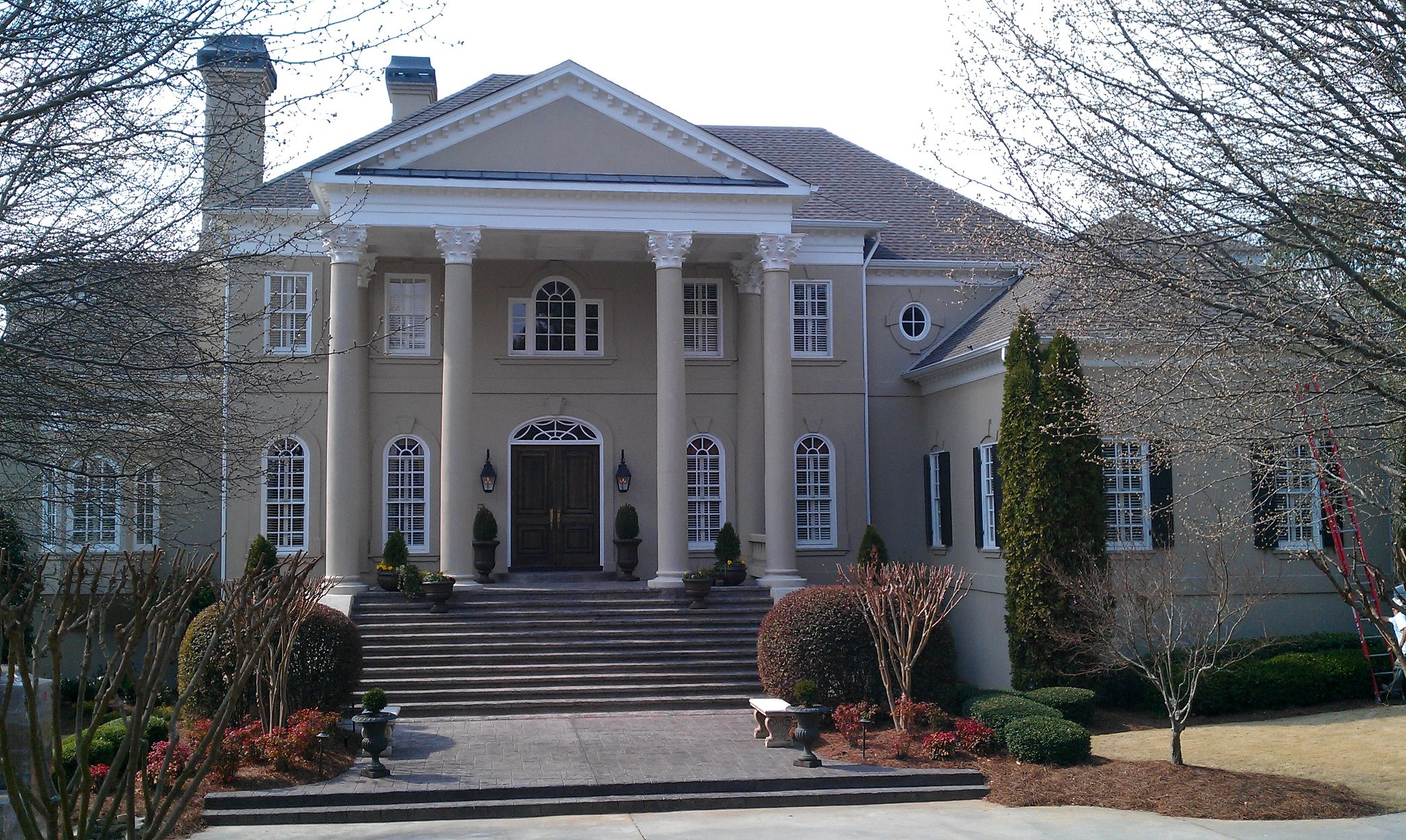
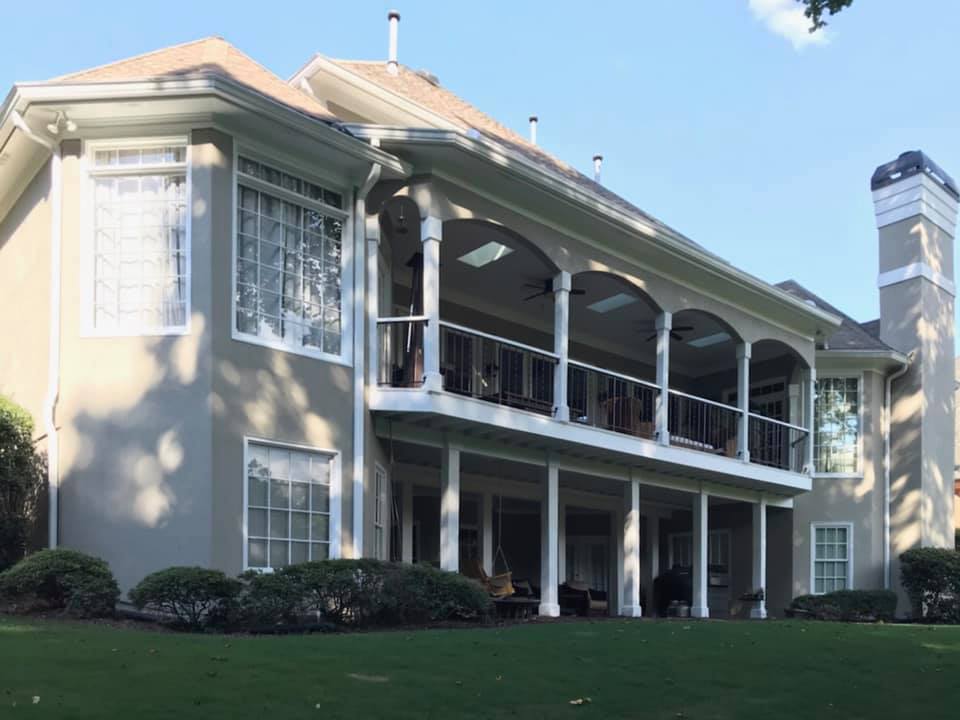
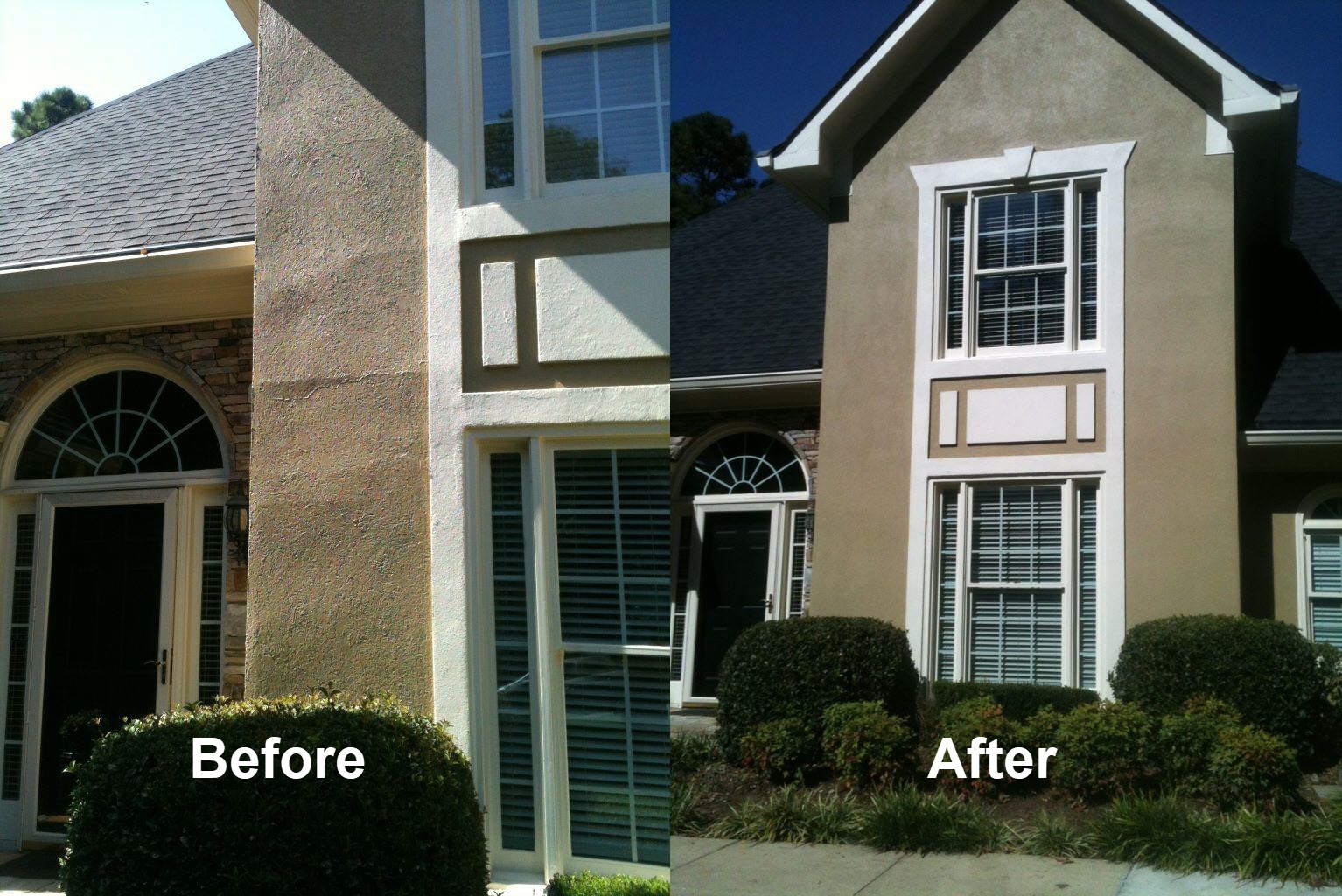
Call Us Today to receive your Free Quote for
Expansion Joints in Woodstock
Serving: Woodstock, Georgia
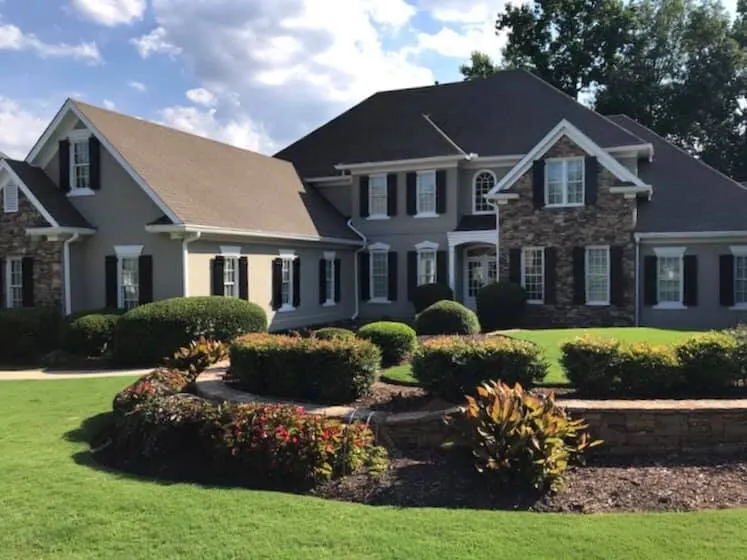
About Woodstock, Georgia
Native Americans were removed from the area.
The Georgia General Assembly incorporated Woodstock as a town in 1897. The community derives its name from Woodstock, an 1826 novel by Walter Scott.
The Woodstock Depot was built in 1912 by the Louisville & Nashville Railroad as the town grew. The line transported cotton, rope, and other agricultural products, as well as passengers. Passenger service ended in 1949.
According to the United States Census Bureau, Woodstock has a total area of 11.3 square miles (29.2Â km), of which 11.2 square miles (28.9Â km) is land and 0.12 square miles (0.3Â km), or 0.92%, is water.
Census | Pop. | Note | %± |
---|---|---|---|
1880 | 92 | — | |
1900 | 276 | — | |
1910 | 442 | 60.1% | |
1920 | 415 | −6.1% | |
1930 | 421 | 1.4% | |
1940 | 389 | −7.6% | |
1950 | 545 | 40.1% | |
1960 | 726 | 33.2% | |
1970 | 870 | 19.8% | |
1980 | 2,699 | 210.2% | |
1990 | 4,361 | 61.6% | |
2000 | 10,050 | 130.5% | |
2010 | 23,896 | 137.8% | |
2020 | 35,065 | 46.7% | |
U.S. Decennial Census |
Race | Num. | Perc. |
---|---|---|
White (non-Hispanic) | 23,727 | 67.67% |
Black or African American (non-Hispanic) | 3,856 | 11.0% |
Native American | 35 | 0.1% |
Asian | 1,529 | 4.36% |
Pacific Islander | 20 | 0.06% |
Other/Mixed | 2,005 | 5.72% |
Hispanic or Latino | 3,893 | 11.1% |
As of the 2020 United States census, there were 35,065 people, 12,878 households, and 8,464 families residing in the city.
As of the census of 2010, there were 23,896 people, 9,580 households, and 6,137 families residing in the city. The population density was 2,715.4 inhabitants per square mile (1,048.4/km). There were 10,298 housing units at an average density of 1,170.2 per square mile (451.8/km). The racial makeup of the city was 79.3% White, 10.2% African American, 0.2% American Indian, 4.5% Asian, 0.02% Pacific Islander, 2.7% from other races, and 3.1% from two or more races. Hispanic or Latino of any race were 9.7% of the population.
There were 9,580 households, out of which 35.2% had children under the age of 18 living with them, 48.8% were married couples living together, 11.7% had a female householder with no husband present, and 35.9% were non-families. Of all households, 29.3% were made up of individuals, and 7.5% had someone living alone who was 65 years of age or older. The average household size was 2.48 and the average family size was 3.12.
In the city, the age distribution of the population shows 26.5% under the age of 18, 6.8% from 18 to 24, 37.4% from 25 to 44, 20.8% from 45 to 64, and 8.5% who were 65 years of age or older. The median age was 34 years. For every 100 females, there were 88.4 males. For every 100 females age 18 and over, there were 84.1 males.
In 2000, the median income for a household in the city was $58,506, and the median income for a family was $65,740. Males had a median income of $48,054 versus $32,798 for females. The per capita income for the city was $25,586. About 2.2% of families and 4.2% of the population were below the poverty line, including 5.0% of those under age 18 and 8.6% of those age 65 or over.
As of the census of 2000, there are 10,050 people, 3,869 households, and 2,627 families residing in the city. The population density is 440.4/km (1,140.4/mi). There are 4,102 housing units at an average density of 179.8 persons/km (465.5 persons/mi). The racial makeup of the city is 89.42% White, 5.05% African American, 0.29% Native American, 1.66% Asian, 0.02% Pacific Islander, 1.94% from other races, and 1.61% from two or more races. 4.94% of the population are Hispanic or Latino of any race.
There are 3,869 households out of which 37.7% have children under the age of 18 living with them, 55.1% are married couples living together, 9.5% have a woman whose husband does not live with her, and 32.1% are non-families. Of all households, 26.1% are made up of individuals and 6.4% have someone living alone who is 65 years of age or older. The average household size is 2.55 and the average family size is 3.10.
In the city the population is spread out with 26.8% under the age of 18, 7.9% from 18 to 24, 39.0% from 25 to 44, 18.3% from 45 to 64, and 8.0% who are 65 years of age or older. The median age is 33 years. For every 100 females there are 92.2 males. For every 100 females age 18 and over, there are 87.4 males.
The median income for a household in the city is $58,506, and the median income for a family is $65,740. Males have a median income of $48,054 versus $32,798 for females. The per capita income for the city is $25,586. 4.2% of the population and 2.2% of families are below the poverty line. Out of the total people living in poverty, 5.0% are under the age of 18 and 8.6% are 65 or older.